Crafting Perfection: Just How to Attain High-Quality Light Weight Aluminum Castings Every Single Time
In the world of light weight aluminum casting, the search of perfection is a continual trip that requires a careful strategy and a keen understanding of the details entailed. Achieving consistent top quality light weight aluminum castings requires a detailed understanding of the procedures, from selecting the appropriate alloy to executing accurate mold layouts and diligently regulating spreading specifications.
Recognizing Aluminum Casting Procedures
Light weight aluminum casting processes, essential in the production market, include the intricate transformation of molten light weight aluminum right into solid types via a collection of meticulously regulated steps. Recognizing these procedures is vital to achieving high-grade aluminum castings constantly - about aluminum casting. The key approaches used in light weight aluminum spreading are die casting, sand spreading, and investment spreading

Each of these processes has its benefits and is chosen based on aspects like intricacy, quantity, and desired surface of the light weight aluminum spreading. about aluminum casting. Recognizing the complexities of these techniques is critical for producers aiming to generate top notch light weight aluminum castings consistently
Picking the Right Light Weight Aluminum Alloy
Picking the suitable aluminum alloy is a critical choice in the manufacturing of top notch light weight aluminum spreadings. The choice of alloy substantially influences the buildings and characteristics of the end product. Different aluminum alloys use differing levels of toughness, corrosion resistance, machinability, and thermal conductivity. When selecting an aluminum alloy for casting, it is necessary to take into consideration the particular needs of the application to ensure ideal efficiency.
One of one of the most frequently made use of aluminum alloys for casting is A356. This alloy supplies exceptional castability, high strength, and good rust resistance, making it suitable for a variety of applications. Additionally, 6061 aluminum alloy is favored for its superior weldability and excellent mechanical buildings. For applications needing high toughness, 7075 light weight aluminum alloy is a prominent selection due to its remarkable strength-to-weight proportion.
In addition to mechanical residential or commercial properties, considerations such as expense, accessibility, and post-casting processes should additionally affect the selection of the right light weight aluminum alloy. By very carefully evaluating these elements, makers can make certain the manufacturing of high-quality aluminum spreadings that satisfy the preferred requirements.
Carrying Out Appropriate Mold Design
Developing an efficient mold design is important for ensuring the effective manufacturing of top notch aluminum spreadings. Appropriate mold and mildew layout plays a considerable function in attaining the desired characteristics of the end product. To implement an effective mold and mildew design, variables such as product circulation, cooling rates, and part geometry should read review be carefully taken into consideration.
One key aspect of mold style is guaranteeing appropriate dental filling and solidification of the aluminum within the mold and mildew dental caries. This entails developing runner and gating systems that assist in smooth metal circulation and prevent flaws such as air entrapment or incomplete dental filling. Furthermore, including cooling channels right into the mold style aids control solidification prices and minimize the danger of porosity or shrinking defects.

Controlling Spreading Parameters
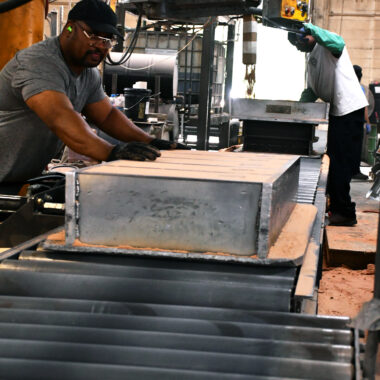
Making Certain Post-Casting High Quality Checks
To preserve the high top quality of aluminum spreadings, extensive post-casting quality checks are vital. After the spreading process is finished, it is crucial to guarantee that the final products satisfy the preferred criteria and requirements. Among the main top quality checks entails inspecting the surface finish of the castings to identify any kind of defects such as porosity, splits, or surface area abnormalities. This visual assessment is commonly supplemented by non-destructive screening approaches like ultrasonic testing or color penetrant examination to detect internal problems that may endanger the integrity of the spreading.
Dimensional precision is one more crucial element that should be verified throughout post-casting top quality checks. Measurements of vital measurements and tolerances ought to be required to validate that the castings adapt to the needed specs. Furthermore, mechanical homes such as solidity, tensile toughness, and influence resistance may require to be examined through product screening to have a peek at this site make sure dig this that the spreadings have the needed toughness and toughness for their desired application.
Conclusion
To conclude, achieving high-quality aluminum spreadings calls for a thorough understanding of the casting procedures, selecting the proper alloy, designing mold and mildews efficiently, managing spreading criteria thoroughly, and conducting post-casting high quality checks faithfully. By following these steps, makers can regularly create light weight aluminum castings that satisfy the highest criteria of top quality and efficiency.
Achieving regular top notch aluminum castings requires a thorough grasp of the processes, from picking the ideal alloy to carrying out precise mold and mildew designs and meticulously controlling spreading parameters. The primary methods used in light weight aluminum spreading are pass away casting, sand spreading, and financial investment spreading.
Investment spreading, also understood as accuracy spreading, includes developing wax patterns that are covered in ceramic to develop molds.Selecting the ideal aluminum alloy is a vital decision in the manufacturing of premium aluminum castings.Ensuring precise control over casting parameters is essential for maintaining consistency and quality in aluminum spreading production.
Comments on “Dive Deep: Insights About Aluminum Casting Processes”